Компания Bugatti будет создавать тормозные суппорты с помощью 3D-принтера
Французский автоконцерн Bugatti станет первым в мире производителем, использующим для разработки тормозных суппортов 3D-принтер. Об этом накануне сообщили представители пресс-центра премиального бренда Bugatti.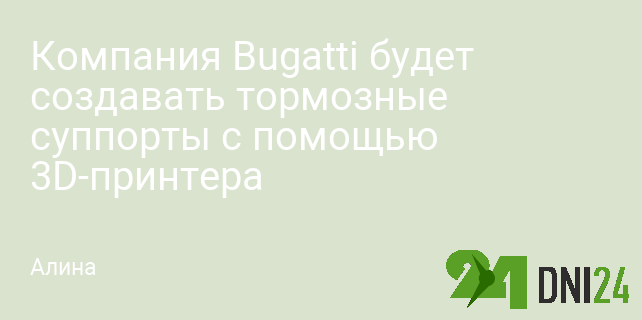
Титановые тормозные суппорты инженеры производят, используя особые лазеры мощностью 400 ватт. На процедуру изготовления у конструкторов уходит 45 часов. Сначала металлический порошок накаляют до 700 градусов, затем его выкладывают 2213 слоями. Каждый тормозной суппорт весит 2,9 кг, это на 2 кг меньше, чем алюминиевый аналог. Титан по своей структуре прочнее алюминия, он выдерживает давление 125 кг/мм.
Как отмечают итальянские разработчики, технология для создания тормозных суппортов на 3D-принтере взята из авиаспортивной индустрии. Отмечается, что компания Bugatti в настоящее время выпускает только один гиперкар Chiron производительностью 1500 лошадиных сил.
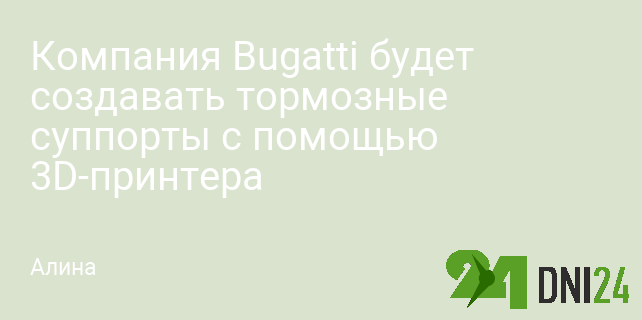
Титановые тормозные суппорты инженеры производят, используя особые лазеры мощностью 400 ватт. На процедуру изготовления у конструкторов уходит 45 часов. Сначала металлический порошок накаляют до 700 градусов, затем его выкладывают 2213 слоями. Каждый тормозной суппорт весит 2,9 кг, это на 2 кг меньше, чем алюминиевый аналог. Титан по своей структуре прочнее алюминия, он выдерживает давление 125 кг/мм.
Как отмечают итальянские разработчики, технология для создания тормозных суппортов на 3D-принтере взята из авиаспортивной индустрии. Отмечается, что компания Bugatti в настоящее время выпускает только один гиперкар Chiron производительностью 1500 лошадиных сил.